製造業の最新トレンドとJDSCの挑戦をテーマに、JDSCの佐藤と田中の対談をお送りします。
田中 龍(株式会社JDSC シニアエキスパート)
日本航空電子工業(株)、(株)インクス、(株)アマダマシンツール、オーストリアANGER-MACHINING gmbh、コンサルファームなどを経て現職。 製造業の核である設計・加工領域での日本初・世界初技術の企画・開発経験を多数有しており、”コト”や体験を軸とした商品企画、オリジナル生産機械やシステム導入などの経験も豊富。業種や業界問わず企画・開発・製造工程に対して圧倒的な成果の創出を実現している。
佐藤 飛鳥(常務執行役員COO)
CONTENT
製造業の現場は今、大きく変わっている
(飛鳥)
まずは、この動画をご覧ください。
(飛鳥)
今ご覧いただいたBMWの例のように、現在世界の製造業の現場は、ロボットによる製造や、デジタルツイン、俗にいうスマートファクトリー化が進んでいます。
私たちは日々、多くの大企業と、さまざまなプロジェクトに取り組んでいます。それらを通じて、大きなインパクトを世に出し、UPGRADE JAPANを実現したいという思いでいます。
私たちの従来からの強みである「三位一体」、つまりビジネスコンサルタント、データサイエンティスト、エンジニア、それぞれのメンバーで連携するのもひとつなのですが、さらなるレベルアップのためには、業界や業務の専門家との連携が必須だと痛感しています。
本日は、業界随一のスペシャリストとして「ものづくりなら、下着からミサイルまで」幅広く製造プロセス変革を進めてきた経験をお持ちの田中龍さんがゲストです。
龍さんご自身のご経験を伺いながら、今のグローバルの最先端の潮流と、そこから遅れてしまっている日本で今から何ができるのか、の価値創出の方法についてもお話していきたいと思っています。
生産の自動化のカギを握る職業、「生産技術」
(飛鳥)
龍さんはこれまで、日本の名だたるものづくり企業の支援をされてきました。「ものづくり」というキーワードから類推すると、やはり機械系の「組み立て製造業」が中心なのでしょうか。
(龍)
組み立て製造業には限定されませんね。「もの」を作っている企業であれば、それがいわゆるtoCのものであろうが、toBのものであろうが、あるいは個社の中でしか使わない特殊製品であろうが、食品や素材まで、かなり幅広に経験してきました。
それこそ下着からミサイルまでですので、半導体や医薬品の製造装置のような特殊性が高い製品も守備範囲です。作るものがなにであっても、基本的には製造工程における機械を作る、自動化する、金属や樹脂、その他の素材を削るなど、いわゆるものづくり全般です。もう少し細かく言うと、「生産技術」とはよくかち合ってしまう「製造技術」を専門としています。
お客さま側に立ち、その製品を作るにあたってどういう作り方をしていかなければならないのか、そのためにはどんな機械設備、どんな仕組み、どんなやり方、どんなノウハウを用いるべきなのか、構想の段階から実装運用まで支援してきました。
(飛鳥)
いきなり細かい点について深堀したいのですが、今のお話に出てきた、「生産技術」と「製造技術」の違いについて教えてください。工場における各メンバーの役割はカレー屋に例えるとわかりやすいと思っているのですが、生産技術の担当と製造技術の担当は、カレー屋に例えるとどういう役割の違いになるんですか?
(龍)
例えばビーフカレーを作る時に、牛肉、玉ねぎ、人参、ルー、お米といった材料を料理して、お皿に盛り付けるまでの一連の工程を考えるのが生産技術です。
この時、例えば「ジャガイモの中でもメークイーンを、かっぱ橋で買ってきたこの包丁を使って皮を剥いて切る」という部分が、生産技術と製造技術の役割が交わるところです。
その包丁がどんな素材で、刃先の角度がこうだから、何度で刃を入れて、力の方向は押すのか引くのか?どれぐらいの速さで、どれぐらいの大きさができるのか?といったことを勘案し、現場の作業に落とし込むのが製造技術です。要は本当のものづくりを計画することであり、根幹ですよね。
機械を使って、例えば工具だったら工具カタログに載っている条件を入力してCAM任せのNCデータを使って加工すれば、それなりのものを作ることができます。ところが、超絶的な技巧が必要なものは、機械任せでは絶対に生産することはできません。どんな機械を使って、どんな風にそれを作っていくのかを徹底的に調べ尽くしたうえで設計することが必要なのです。
つまり、包丁の素材となっている金属材料の組織組成や工場での生産の仕方、圧延方向や焼き入れによってこの形になっている、刃先にはこういう物理的な特性があるというところまで全部理解するんです。どこまで深く入り込んで考えられるかが勝負になってくる世界なんですよね。
(飛鳥)
なるほど。では製造技術の方たちは、今どきのキーワードで言えば、例えば工場の「自動化」だとか「ロボット導入」だとか「完全自動生産」とか、そういった検討を担当すると理解してよいのでしょうか。
(龍)
そうですね。ですから優れた製造技術者の頭の中をAI化して、最適化案を自動でレコメンドするようなことができればいいですよね。物理法則、物理特性理論のような幅広い知見をベースに、AIが最適化した方法に則ってものがどんどん加工され、どんどん組み合わされて製品ができる世の中になります。
(飛鳥)
具体的な議論をさせてください。
先日、ある大手食品会社様から、完全自動化、完全自動生産についての相談がありました。とにかく工場の現場の人手が不足しているそうです。これまではコスト削減のためのロボティクスだとか自動化だと言っていましたが、今はもはや夜間や土日からでも段階的に完全自動化を実現しないと十分な量の食品を生産できない、事業の継続性が危ういという状況まできているとのことでした。いやー、昨今、同じような話を聞くことが、本当に増えましたね。
では龍さん、例えば食品においての完全自動生産の難しさや課題は、どのあたりにありそうだと思いますか?
(龍)
具体例をイメージできた方がいいので、例えばビールとしましょうか。製造技術のところでもお話したように、物質の特性に着目して、ビールがどういうケミカルの変異を起こしていくか、時間的な変異、温度管理、環境要因など、どんな要素に関連付いて何がどう変わっていくか、そのメカニズム、関連性を解くことが必要ですね。
これは、データとして考えることができると思うんですよ。ちなみに、私の言う「データ」は必ずしも数字じゃなくてもいいです。例えば農家の人は「作物の顔を見て判断する」と言うわけですよ。僕たちにはよくわからないけど、実際その人が見て判断していることと作物の生育は関連しているじゃないですか。顔、つまりは画像ですかね。それと同じで、鉄を削ろうがビールを作ろうが野菜を育てようが、何かに関連付けられた事象の中身を、データとして分解する思考を持てるかどうかだと思います。
職人の感覚≒頭脳労働のAI化に向けて
(龍)
では、人間でなければできない作業とは何かというと、やはり熟練の職人の仕事ですね。職人がやっている作業は、頭脳労働と単純頭脳労働と単純労働に分けられます。
頭脳労働というのは、「これどうしようかな?こうしようかな?」と深く考えてやること。単純頭脳労働というのは、いくつかの選択肢からルールベースで選んで作業すること。単純労働というのはただ作業さえすればできてしまうこと。これは個人の熟練度合いによってレベルがどんどん上がってくると思います。
ですから適宜ヒアリングなどをしながら、現状を解析、分析して、それをデータと関連付けながら整列させてやると、十分に仕組みに落とせるんじゃないでしょうか。
(飛鳥)
私お酒に弱いのでイメージが不十分ですが、例えばビールの醸造所の責任者は、醸造度合いを温度変化やその時間、あるいは匂いや見た目の色や泡の具合などで確認している、みたいな想像をしながらお聞きしました。その職人の感覚のようなものを、今言ったような項目のデータによって判断の根拠とできるのであれば、判断の工程のAI化ができますよね。
(龍)
方向としてはその通りだと思います。
他の事例をお話ししましょうか。私はもともと金型職人上がりです。例えば、金型の職人の世界だと、「金属に溝が掘ってあって、その溝に別の金属をはめこんだ状態で、ひっくり返しても落ちないけれど、引っ張れば抜ける」という、微妙な寸法を求められることがあります。
職人の中ではそれを「しっくりはまる」と表現します。抽象的な表現ですが、全部測ってデータ化してみると、例えばこの隙間が3ミクロンで、機械加工された目の方向がどうで、その面粗さがどれぐらいで、さらにもう一段掘り下げた面相がどういう状態の時に「しっくりはまる」と職人が判断しているということがわかりました。つまりこれは、データなんです。
それならその状態を自動で実現するためには、どういう機械、どういう工具を使って、どういう条件でどういう加工をすればよいか、わかりそうですよね。実はこれ、20年近く前に「インクス」という会社でやっていたことです。でも20年前にそこまでできていたものですから、今はもっと高度に、または幅広な工程を対象にできるんじゃないのか?という話なんです。
(飛鳥)
今、インクスという会社の名前が出ました。30歳前後の皆さんはご存じないかもしれませんが、インクスというベンチャーは、僕が就職活動をしていた2003年ぐらいに、日本の製造業を変えると世の中を席巻していたすごいベンチャーだったんです。その会社が出版した「インクス流」という本は、製造業チームで先日回し読みをしましたが、今読んでも全然古くない、まさに今の時代に求められている考え方だと感心するぐらいでした。
(龍)
実際にはやりの部品製作サービスや台湾のCIMFORCEなどは 実質的に当時のインクスのシステムとほぼ同じです。他に例えば、 SHIFT社やコアコンセプトテクノロジー社など、勢いのある企業の経営層でインクス卒業生が多いですね 。
(飛鳥)
龍さんから見ると、世の中が変わるのに20年かかってしまったという感覚だと思いますが、いずれも今の製造業にインパクトを創出していますね。
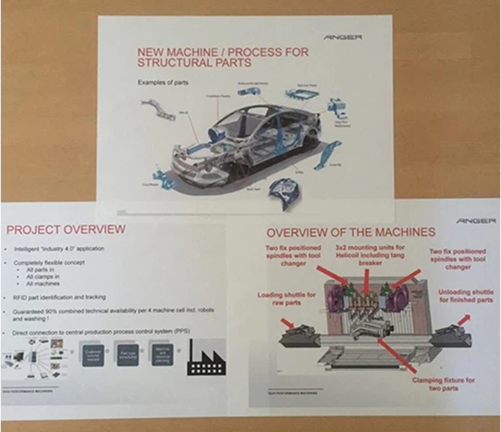
田中龍が ANGER-MACHINING時代に企画開発した超複合生産システム
Industry4.0、本場欧州と日本の解釈の違い
(飛鳥)
話は戻りますが、龍さんの実績は自動車業界も多いですよね。例えば冒頭に流した動画のBMW は、龍さんがヨーロッパに行っている時期に担当されていたのでしたっけ?それとも日本にいる時ですか?
(龍)
BMWとは、オーストリアのANGER-MACHINING社に在職していた時代に、特に深くお付き合いさせていただきました 。
ANGER-MACHININGでは、最初はエンジンブロックやトランスミッション周りの生産システムの共同開発から始まり、徐々に開発やデジタルツインやメタバース系のところまで協業範囲を広げていました。ですから私は、自動車の商品企画から生産、製造、販売まで一通りやったことになります。
欧州メーカーの場合は、売った商品に何かトラブルが起きた時に、ユーザーの行動履歴からどの部品にどんな負荷がかかってどう壊れたかが即座にわかるように、仕組みを構築しています。先ほど少しお話したように、加工面がこういう状態だから隣の部品との摩擦力が大きくて破損してしまったのではないかというところまで、瞬時に原因分析ができるような仕組みになっているんです。
(飛鳥)
龍さんが欧州にお住いの期間には、「インダストリー4.0」なんて言葉も生まれましたよね。まさにこのようなコンセプトを実地で感じる機会が多かったのではないかと思います。具体的な経験について教えてください。
(龍)
当初は目からウロコでしたね。日本ではそもそもインダストリー4.0の理解のされ方が間違っています。私がいたオーストリアの生産システムメーカーは数百人ぐらいの小規模な企業でしたが、システム屋さん含めて、それぞれの会社が基幹システム、生産管理システム、稼働管理システム、あるいはシックスシグマまで測定できるインライン計測システムを全部持ってるんですね。
それをユーザーの基幹システムにつなげれば、社長からアルバイトまでリアルタイムで何がどこでどうなっているか、全部見ることできるようになる。それならつなごうよという概念運動がインダストリー4.0なんですよ。それはそのまま、デジタルツインのベースになりますよね。
そのデジタルツインを明確化するために、仮想空間上、メタバース上で、先ほど動画で見たような、何の制限も受けない理想的な状態を作る。日本でいうと流動解析だとかエフエム解析とかです。何の制限も受けない状態の中で、こういうふうにものを作っていくべきだ、こうあるべきだという理想に対して、リアルがどうなのか見られるようになる。これがデジタルツインであり、インダストリー4.0の中身です。
スマートファクトリーというのは、さらに仮想空間上で構築したものをタイムラプス的に過去に遡ったり未来に行ったりできるので、今起きている事象がちょっとおかしいぞとなった時に、過去に遡ってリアルの状態と見比べて原因を突き止め、指令を出して、少し先の未来を変えられるものなんです。そこの理解が欧州と日本では全く異なっていると感じますね。
日本で、スマートファクトリー化を進めるには?
(飛鳥)
欧州がオリジンなのでそれが本家として正しいとして、日本でスマートファクトリーやデジタルツインに関する議論をしている時、どのようなギャップを感じることが多いですか?
(龍)
初回の議論の時から感じています。ですがそれは悪いことではなくて、日本は日本のDXがあればいいと思うんですよ。お客さまそれぞれに対して、御社のスマートファクトリー、どういう形にしますか?という議論から始めていいと思うんですね。
ヨーロッパに6年いた私から見たら、日本のDXってただのデジタライゼーションでしかないんですよね。DXというのはトランスフォーメーションですから、何がどれだけ変わりましたか?という範疇で考えると、日本を代表する超大企業ですら本当の意味でのDXはできてないですよね。
(飛鳥)
それは特に製造工程、特に工場の製造技術が昔と変わってないということですか?
(龍)
そうです。以前、ある自動車会社の工場で「田中さん、機械にセンサーつけたから見てください」と言われて見に行ったら、1台の機械にセンサーが90個も付いてるんですよ。ビックリしました。90通りの振動データが見えるらしいです。
が、私、3秒後に何言ったかっていうと、「でも、機械は止まるでしょう?」って。すると自信満々に「はい」って言うんですよね。なぜ止まったか、この90個の波形を調べれば見えるようになるというんですが、じゃあどう見るのか?どうそれを生かすのか?ということが考えられていない。
例えば工作機械でX軸、Y軸、Z軸があって、Z軸が壊れた時、その原因は3ヶ月前のX軸の小さな振動である、というような分析をしなきゃいけないんですよ。3ヶ月前のその時に誰がどこで何をやっていましたか?どんなことをやっていましたか?どんなふうにやっていましたか?ということを解析しなければ、トラブルは回避できないんですよね。
(飛鳥)
データはそこまで必要ないし、逆に90個あるからといって必要なデータが全部あるかというと、そうでもなかったりするんでしょうか。
(龍)
そうです。機械構造、機械の特性がわかれば、そもそもセンサーが何個必要かわかるんですよ。現場で製造に携わっている人間が、自分が使っている機械のことを何もわかってないことがまず問題です。これは企業の教育の問題でもありますが。
(飛鳥)
そうすると、例えばその機械の構造から考えたら、X軸、Y軸、Z軸のデータがないと、そもそも話にならないよねとか、その駆動部自体がどう影響してくるかまで考えれば、必要な場所って決まってくるよねということですか?
(龍)
自動車であれば、エンジンからプロペラシャフトというのが出て、デフにつながって駆動します。工作機械では、プロペラシャフトに相当する部分としてモーターがあって、ボールネジがあって、そこに稼働するテーブルがあります。構造は全く同じで、モーターとエンジンが回った時にこのインプットシャフトがたわみながら伝達されていくんですね。ボールネジとか自動車のプロペラシャフトって、実はすごくたわんでいるんです。そのたわみの振動がモーターの動きに対してどのように働くかが見えてくると、いろんなことがわかってきます。
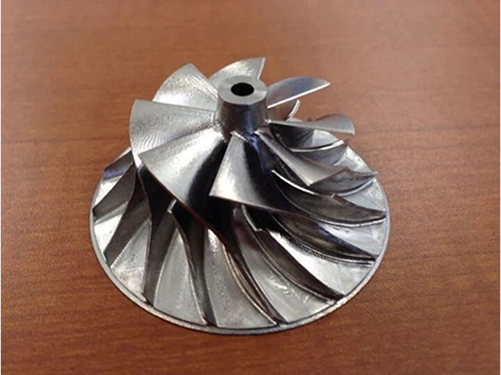
田中龍が自作した自動車用タービン
日欧の違い、「マイスター」は「職人」とは違う???
(飛鳥)
ここで、「欧州ではどこまでデータの連携がされているのか、実例を知りたいです」という質問が来ています。
例えば龍さんがいらっしゃった ANGER-MACHINING は300人くらいの企業ですが、どのぐらいのレベルまでできていたのか、程度を知りたいんじゃないかと思います。
(龍)
私のいたメーカーだと、例えばメルセデスベンツからエンジンブロックを生産するための機械がほしいと注文を受けたら、先方から対象となる部品の3Dデータをいただいて、自社のCADシステムの中で、機械のフレームがあって、どこに置いてどういうふうに金属の塊から形にしていこうか、干渉チェックとか全部やるんですよね。
日本の場合だと、そういうものは担当する会社や部門ごとにそれぞれCADCAMシステムがあって、形が変わる度にCAD上で設計して、CAMシステムで機械のNCデータを作って、加工して次工程に流していきます。
私のいた会社では、その中でやったことがそのままNCデータになっちゃうので、お客さまに納めたその日に、スタートボタンを押せばすぐに生産できるんです。さらに作っている最中も、メルセデスベンツの方で設計変更があったらオンラインで我々の会社の中のデータが変わってくれるから、そこに携わる工作機械的な事象も自動的に設計変更が起きる。そういうシステムが構築されてるんですね。
(飛鳥)
これ、パッと聞くと当たり前に思えるかもしれませんが、日本ではそもそも企業間で3D図面が渡されることがないじゃないですか。3DCADで作ったデザインをなぜか2Dに起こして2Dの図面としてお渡しして、サプライヤー側はサプライヤー側でその2D図面をもとにNCデータに起こし直している。商習慣を変えていくにあたって、何か明確なボトルネックはあるんですかね?
(龍)
単に、民族的なものでしょうね。
(飛鳥)
「紙大好き」みたいなやつですか?
(龍)
要は、欧米の「マイスター」と日本の「職人」の違いです。日本は職人さんの腕頼りですよね。「今日は彼がいないからこれはできない」ということが往々にしてよくあります。だけど欧米のマイスターって、自分の持っている超絶的な技能をどうやったらみんな一緒に使うことができるかを考える人たちなんですよ。
(飛鳥)
それは結構意外ですね。職人とマイスターが目指す姿は一緒だと思っていました。
(龍)
全然違いますよ。例えば軍事的な話でいえば、一人の強い兵隊さんがいればみたいなイメージってあると思うんだけど、実際にはアメリカの海兵隊なんて、いかに並列で連動してみんなで攻めていくかを考えています。そういう文化的な側面は結構大きいんじゃないかな。
ですから、日本のデジタルツイン、スマートファクトリーをどうしていきましょうか?という点においては、逆にそこは守るべきところなのかもしれないですよね。それがないと、標準化ではなく平準化になってしまうので。物流やそれに近しい分野においては平準化は必要かもしれないですけど、ものづくりにおいては平準化って他と差がなくなってしまうということなんで。
(飛鳥)
今の、職人とマイスターの例はものすごく面白いと思いました。ドイツのマイスター制度でも、自分の超絶技術をいかに広めていく、場合によっては形として残していくことを指しているんですか?
(龍)
そうそう。だから、「あの人がいるからできる」ではなく、「あの人がいたからこれができる」というのが100年後、200年後に残るか残らないかという話なんですよね。
例えば、以前、日本を代表するコネクタメーカーの研削加工という工程で私がコンサルティングをした時にやったのが「マイスター化」だったんです。それぞれが持っている超絶的な技巧をみんなで使えるようにしようよって。最初はものすごい反発を食らいましたけど、まずそこに手を付けたんですね。他は何にもしてないんですよ。使えるようにしましょうとしただけで、生産効率が倍になりました。
(飛鳥)
具体的にはどんなことをやったんですか?先ほどの説明でもあったように、頭を使って判断する労働では、そもそもセンサー自体が通常の人ではセンシングしていないものを計測しているし、センサー自体の質が異なるんじゃないんですかね。そうすると、こうやったらいいんだよと言語化したところで、自分の体にそのセンサーを積んでないということもあると思うし、またはコントロールしようとしても今度はコントローラー側がそこまでの精度にないということもあると思うんですけど、どういう方法でその超絶技巧を模して横展開するのでしょうか。
(龍)
すごくいいことを聞いていただきました。職人をエンジニア化したんです。まず、職人さんに「あなたたちがやっていることはこういうことだよ」と、さっきお話したような理論理屈を教えたんですよ。
使う砥石の物質、例えばダイヤモンドやCBN、それらをつなぎ止めるボンドがどういう材質でできているというような構造的、物質的な知識。それから、どれぐらいの速さで金属に当たった時に、金属表面でどんなことが起きるのかという研削加工に必要な研削理論。そういったことを全部教え込んで、今あなたたちがやっている超絶的な技法は、理論的に見ればまだまだ安全率の高いところにいるんですよ、だからもうちょっと伸ばせますよね?と教えました。
その上で、全員に「俺はこういう時にこう感じてる」という、いわゆる指先の感覚技術をバーッと書いてもらって、あ、ここは一緒だったね、ここ違うねと確認して。入社2、3年目の子たちが何十年のベテランと同じことをやるには、こういう治具を作ってやればできるよね、ということをやりました。
(飛鳥)
なるほど。技術と技術感覚を言語化して、その感覚を数値としても揃えにいくということなんですね。
(龍)
「職人/マイスター」と言えば、日本だと大田区に、超精密加工、積層造形、レーザーから職人手仕上げ彫刻が出来るような、それぞれの領域において素晴らしい技術を持った企業があります。私も個人的にずっと付き合ってきました。
金属加工、樹脂加工、金型製作、機械装置や自動化システム製作まで対応できるようになると、製造工程において貢献できる幅が大きく広がります。
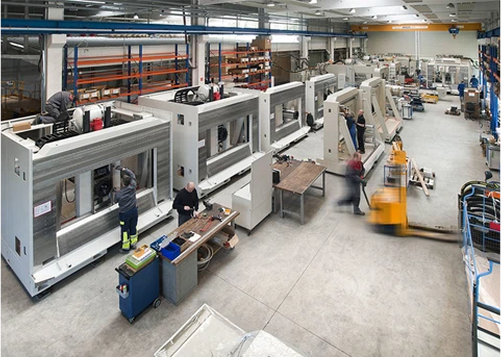
田中龍の主催する製造エンジニアリングネットワーク、JDSCの協力工場の一つ
(再び)日本で、スマートファクトリー化を進めるには?
(龍)
話を戻しますが、製造の工程だけじゃなくて、工場のシミュレーションも同じです。例えば、ダイキンさんの工場などは、今みたいな考え方とデジタルツインを組み合わせてやれば、結構簡単にできるでしょ?
(飛鳥)
先日、ダイキンさんの大阪堺にある業務用空調の工場と、滋賀の草津にあるルームエアコンの工場を龍さんと一緒に見てきましたね。前者はダイキンさんの中では最新鋭の工場だったんですが、龍さんから「飛鳥さん、あそこは○○な手法を使っているけれども、○○を採用すればまだ改善する可能性があって…」と20回ぐらい言われました。
(龍)
そうですね。もちろんダイキンさんも諸々の前提条件がある中で今の生産方法を採用しているのでしょうが、ああいう工程をゼロから設計したいですね。ダイキンさんの工場でいえば、エアコンの室外機を組み立てていく工程で、ベースにいろんな配管や電子機器やモーターを積み重ねていくわけじゃないですか。まず仮想空間上でその工程を完璧に作り上げて、それを実現するためには工場内でどういう動線でどういうふうにしていったら、一番うまくできるのか?
さらにその作業は人がやるのか、ロボットがやるのか?とリアルを理想にどう近づけていって、どう管理監視するのか。センシングしたなら、そのセンシングされたデータをどこにどういうタイミングでフィードバックしてやれば次の工程、さらに先回って何がしかのリアルタイムの指示ができるのか、もうそれだけだと思うんですよ。それがダイキンさんのスマートファクトリーなのかなと思います。
(飛鳥)
ある意味、日本流であり、ダイキン流ということなのかもしれないですね。単に欧州を模せばいいだけでもないですから。
(龍)
この間見たダイキンさんのロウ付けの工程や配線配管を付ける工程を例にしましょう。決められた人数、決められたタクトタイムで作業をこなす工程が複数ありましたよね。例えばですが、与えられたタクトタイムの中で13秒で終わる人と18秒で終わる人がいるのが一般的です。これを全員13秒にしてやることができれば、そのステージは20秒から15秒に落とせますよね。
そうすると全体のタクトタイムが5秒縮むわけですよ。もしそこが工場内全体の中のクリティカルパス、最も時間のかかる部分だとしたら、そこを直すだけで生産効率が数十パーセント向上できるわけです。そこをAIとか使って見せてやりながら実行していきましょうよっていう話だと思うんですよ。
(飛鳥)
それは作業者間のボラティリティがある中で、いかに早くしていくかということですか?それともボラティリティを踏まえた上で、その混合生産をうまく調整するということでしょうか。
(龍)
どちらでもいいと思います。必ずしも同じものを流す必要はなくて、あえてもう1分止めて30個同時に出したっていいわけですから。
(飛鳥)
なるほど、そうか。特にダイキンさんは変種変量生産だから、組み合わせ最適をきちんと作れるエンジンさえあれば、個人のボラティリティ、またその一個一個のパーツ作りに対しての難度とか、時間の差を吸収できる可能性があるんですね。
(龍)
今日話してきたように、エアコン作ろうが下着作ろうがミサイル作ろうが一緒ですよ。私の場合、工作機械生産システムという軸があって、工作機械からものを見た時に、相手が食品だろうが石だろうが繊維だろうが半導体だろうが飛行機だろうが変わらないんです。要は方法論の条件的なところ。
オングストロームレベルの話かマクロの話かという差はあれど、何も変わらないんですよね。皆さんそれぞれに得意なものの見方があるはずだろうから、それをベースにして、すべての事象を捉えられるような訓練をしてもらえれば、一つの物事に対して全天球方向から見えるようになるわけですよね。
(飛鳥)
それは心強いですね。正直言うと、龍さん流のものの見方をゼロから脳内に構築するのは結構ハードルが高いと思っていました。そうではなくて、今持っている自分の見方や強みに、このものづくりの視点を組み合わせて、自分なりの見方をすれば十分なんだよというメッセージは、すごく心強いというか、ありがたいです。
(龍)
そうなんですよ。だから飛鳥さんだったら全部の物事をカレーライス目線で見ればいいんです。そういう目線であらゆるものを見られるようになれば、必ず共通するものがあるので。
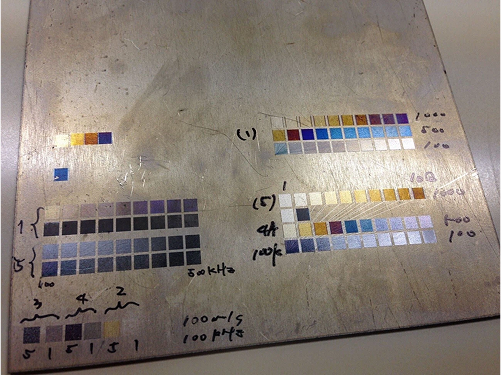
田中龍が作成した特定の色だけを反射するマイクロ構造のレーザーカラーリング
日本における工場のロボット化に向けて
(飛鳥)
ひとつ教えてください。今、テスラはロボットを頑張ってるじゃないですか。あのようなロボティクスが日本の市場に定着するのは何年後ぐらいだと思いますか?
オペレーションの仕組みは変わってくるわけじゃないですか。ハードがあったとしてもソフトは追求していかなければいけないので。5年後、10年後を見据えて、どこにどういうアプローチを考えていくべきでしょうか。
(龍)
おそらく、特定の自動車業界、特定のモデルの生産ラインにおいては、3年後には実用化できると思います。ただ、生産数によって製造業でも物流側の自動化システムを入れなきゃダメだと思う。例えば、2秒に1個ものが出てきますというレベルのものだと、物流の自動化システムを組み合わせないとダメですね、更にhumanoidが実用化されたらラインという概念も変わってしまう。
(飛鳥)
工場の中だけやってもダメで、外と連動させないと効果が薄まってしまいますからね。部品調達等の入り口と、出荷等の出口をちゃんと作り込みしていかないと、結局歩留まりが発生して、工場において余計な面積を取ることになる。それなら結局、人を入れた方がいいじゃんって話になっちゃいますね。
(龍)
生産工場の中身も、いわゆる工場内物流だと割り切って考えないとダメな時代になってきています。例えば、一品一様の金型しか毎日流れてない工場と、自動車工場のように同じものを一日十万個作らなきゃいけないっていう工場だと、投入する技術も物流システムも全く違うものになる。生産数に応じて物流側のシステム思想を入れなきゃいけないという場合もある。humanoidが実用化されたら物流ラインや製造ラインを構築すること自体が不要なってくる。では実際にライン化するのか屋台方式にするのか、どのように設備を配置するのかなど、その区分けを判断するAIツールがあったとしたら、結構バズると思う。まだまだできることって本当にたくさんあるんですよ。